Oil-embedded flanged sleeve bearings are designed to enhance equipment reliability and longevity by combining lubrication and structural support in a single component. Below is a detailed explanation of how they achieve this:
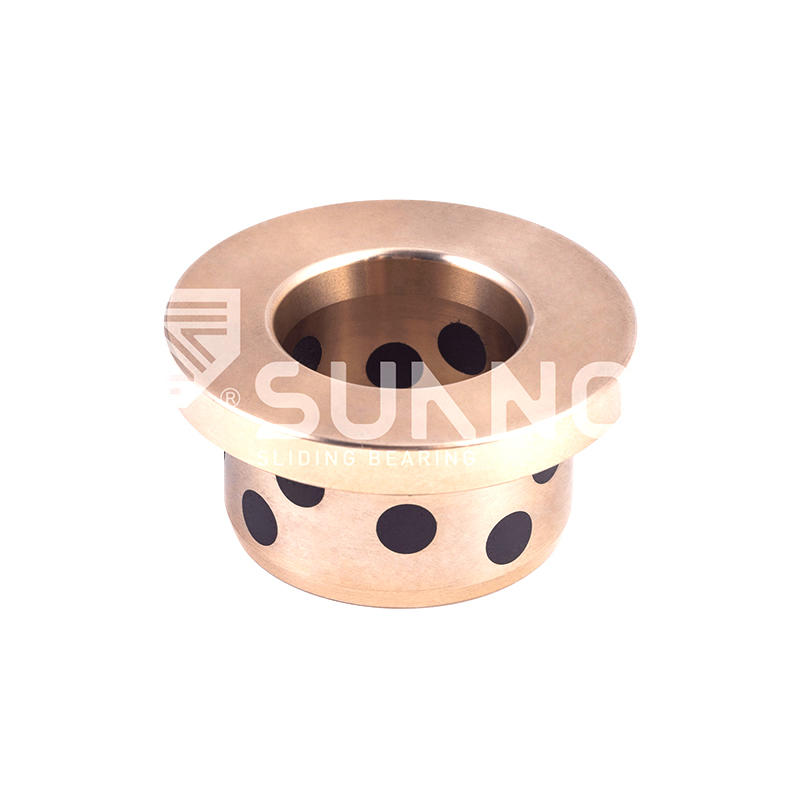
JFBB Metric Self-lubricating Oilless Graphite Flanged Bearings Bushings
1. Self-Lubricating Design
Embedded Lubricant: The bearing material contains microscopic pores filled with oil or grease. As the bearing operates, friction generates heat, causing the lubricant to seep to the surface, forming a protective film.
Reduced Wear: This continuous lubrication minimizes metal-to-metal contact, reducing friction and wear on both the bearing and mating surfaces.
Example: In a conveyor system, oil-embedded bearings ensure smooth rotation of rollers even under heavy loads, preventing premature failure.
2. Flanged Structure for Stability
Alignment & Load Distribution: The flange acts as a mechanical stop, preventing axial movement and ensuring proper alignment. This reduces stress on the shaft and housing, distributing loads evenly.
Vibration Damping: The flange absorbs minor misalignments and vibrations, protecting the bearing and connected components from fatigue.
Application: In automotive steering systems, flanged bearings maintain precise control by resisting axial loads and dampening road-induced vibrations.
3. Corrosion & Contamination Resistance
Material Selection: Bearings are often made from stainless steel, bronze, or polymer composites, which resist rust and chemical degradation.
Sealed Design: The flange can incorporate seals to block dirt, moisture, and debris, preserving lubricant integrity.
Example: In food processing machinery, sealed flanged bearings prevent contamination and corrosion, ensuring hygiene and durability.
4. Maintenance-Free Operation
No Relubrication Needed: The embedded lubricant eliminates the need for manual greasing, reducing downtime and labor costs.
Longer Service Intervals: Bearings can operate for thousands of hours without maintenance, ideal for hard-to-access applications like wind turbines.
5. Enhanced Load Capacity
Material Strength: High-performance polymers or composites withstand heavy radial and axial loads, preventing deformation.
Flange Reinforcement: The flange adds rigidity, enabling the bearing to handle higher loads without compromising performance.
Use Case: In agricultural machinery, reinforced flanged bearings endure harsh conditions and variable loads during planting or harvesting.
6. Cost Efficiency Over Time
Reduced Downtime: Fewer replacements and repairs lower operational costs.
Energy Savings: Lower friction reduces power consumption, improving efficiency.
Example: In industrial fans, oil-embedded bearings cut energy use by 10–15%, lowering long-term expenses.
Comparison with Traditional Bearings
Feature |
Oil-Embedded Flanged Sleeve Bearings |
Traditional Bearings |
Lubrication |
Self-lubricating (maintenance-free) |
Requires regular greasing |
Alignment |
Flanged design ensures stability |
Relies on external fixtures |
Corrosion Resistance |
High (material + sealed design) |
Varies; often needs additional protection |
Load Capacity |
High (reinforced structure) |
Moderate; prone to deformation |
Maintenance |
Low/none |
High (frequent relubrication) |
Cost Over Lifespan |
Lower due to reduced downtime |
Higher due to replacements/repairs |